4.3: Piping and Instrumentation Diagrams - Location of Controls and Standard Control Structures
- Page ID
- 22384
\( \newcommand{\vecs}[1]{\overset { \scriptstyle \rightharpoonup} {\mathbf{#1}} } \)
\( \newcommand{\vecd}[1]{\overset{-\!-\!\rightharpoonup}{\vphantom{a}\smash {#1}}} \)
\( \newcommand{\id}{\mathrm{id}}\) \( \newcommand{\Span}{\mathrm{span}}\)
( \newcommand{\kernel}{\mathrm{null}\,}\) \( \newcommand{\range}{\mathrm{range}\,}\)
\( \newcommand{\RealPart}{\mathrm{Re}}\) \( \newcommand{\ImaginaryPart}{\mathrm{Im}}\)
\( \newcommand{\Argument}{\mathrm{Arg}}\) \( \newcommand{\norm}[1]{\| #1 \|}\)
\( \newcommand{\inner}[2]{\langle #1, #2 \rangle}\)
\( \newcommand{\Span}{\mathrm{span}}\)
\( \newcommand{\id}{\mathrm{id}}\)
\( \newcommand{\Span}{\mathrm{span}}\)
\( \newcommand{\kernel}{\mathrm{null}\,}\)
\( \newcommand{\range}{\mathrm{range}\,}\)
\( \newcommand{\RealPart}{\mathrm{Re}}\)
\( \newcommand{\ImaginaryPart}{\mathrm{Im}}\)
\( \newcommand{\Argument}{\mathrm{Arg}}\)
\( \newcommand{\norm}[1]{\| #1 \|}\)
\( \newcommand{\inner}[2]{\langle #1, #2 \rangle}\)
\( \newcommand{\Span}{\mathrm{span}}\) \( \newcommand{\AA}{\unicode[.8,0]{x212B}}\)
\( \newcommand{\vectorA}[1]{\vec{#1}} % arrow\)
\( \newcommand{\vectorAt}[1]{\vec{\text{#1}}} % arrow\)
\( \newcommand{\vectorB}[1]{\overset { \scriptstyle \rightharpoonup} {\mathbf{#1}} } \)
\( \newcommand{\vectorC}[1]{\textbf{#1}} \)
\( \newcommand{\vectorD}[1]{\overrightarrow{#1}} \)
\( \newcommand{\vectorDt}[1]{\overrightarrow{\text{#1}}} \)
\( \newcommand{\vectE}[1]{\overset{-\!-\!\rightharpoonup}{\vphantom{a}\smash{\mathbf {#1}}}} \)
\( \newcommand{\vecs}[1]{\overset { \scriptstyle \rightharpoonup} {\mathbf{#1}} } \)
\( \newcommand{\vecd}[1]{\overset{-\!-\!\rightharpoonup}{\vphantom{a}\smash {#1}}} \)
\(\newcommand{\avec}{\mathbf a}\) \(\newcommand{\bvec}{\mathbf b}\) \(\newcommand{\cvec}{\mathbf c}\) \(\newcommand{\dvec}{\mathbf d}\) \(\newcommand{\dtil}{\widetilde{\mathbf d}}\) \(\newcommand{\evec}{\mathbf e}\) \(\newcommand{\fvec}{\mathbf f}\) \(\newcommand{\nvec}{\mathbf n}\) \(\newcommand{\pvec}{\mathbf p}\) \(\newcommand{\qvec}{\mathbf q}\) \(\newcommand{\svec}{\mathbf s}\) \(\newcommand{\tvec}{\mathbf t}\) \(\newcommand{\uvec}{\mathbf u}\) \(\newcommand{\vvec}{\mathbf v}\) \(\newcommand{\wvec}{\mathbf w}\) \(\newcommand{\xvec}{\mathbf x}\) \(\newcommand{\yvec}{\mathbf y}\) \(\newcommand{\zvec}{\mathbf z}\) \(\newcommand{\rvec}{\mathbf r}\) \(\newcommand{\mvec}{\mathbf m}\) \(\newcommand{\zerovec}{\mathbf 0}\) \(\newcommand{\onevec}{\mathbf 1}\) \(\newcommand{\real}{\mathbb R}\) \(\newcommand{\twovec}[2]{\left[\begin{array}{r}#1 \\ #2 \end{array}\right]}\) \(\newcommand{\ctwovec}[2]{\left[\begin{array}{c}#1 \\ #2 \end{array}\right]}\) \(\newcommand{\threevec}[3]{\left[\begin{array}{r}#1 \\ #2 \\ #3 \end{array}\right]}\) \(\newcommand{\cthreevec}[3]{\left[\begin{array}{c}#1 \\ #2 \\ #3 \end{array}\right]}\) \(\newcommand{\fourvec}[4]{\left[\begin{array}{r}#1 \\ #2 \\ #3 \\ #4 \end{array}\right]}\) \(\newcommand{\cfourvec}[4]{\left[\begin{array}{c}#1 \\ #2 \\ #3 \\ #4 \end{array}\right]}\) \(\newcommand{\fivevec}[5]{\left[\begin{array}{r}#1 \\ #2 \\ #3 \\ #4 \\ #5 \\ \end{array}\right]}\) \(\newcommand{\cfivevec}[5]{\left[\begin{array}{c}#1 \\ #2 \\ #3 \\ #4 \\ #5 \\ \end{array}\right]}\) \(\newcommand{\mattwo}[4]{\left[\begin{array}{rr}#1 \amp #2 \\ #3 \amp #4 \\ \end{array}\right]}\) \(\newcommand{\laspan}[1]{\text{Span}\{#1\}}\) \(\newcommand{\bcal}{\cal B}\) \(\newcommand{\ccal}{\cal C}\) \(\newcommand{\scal}{\cal S}\) \(\newcommand{\wcal}{\cal W}\) \(\newcommand{\ecal}{\cal E}\) \(\newcommand{\coords}[2]{\left\{#1\right\}_{#2}}\) \(\newcommand{\gray}[1]{\color{gray}{#1}}\) \(\newcommand{\lgray}[1]{\color{lightgray}{#1}}\) \(\newcommand{\rank}{\operatorname{rank}}\) \(\newcommand{\row}{\text{Row}}\) \(\newcommand{\col}{\text{Col}}\) \(\renewcommand{\row}{\text{Row}}\) \(\newcommand{\nul}{\text{Nul}}\) \(\newcommand{\var}{\text{Var}}\) \(\newcommand{\corr}{\text{corr}}\) \(\newcommand{\len}[1]{\left|#1\right|}\) \(\newcommand{\bbar}{\overline{\bvec}}\) \(\newcommand{\bhat}{\widehat{\bvec}}\) \(\newcommand{\bperp}{\bvec^\perp}\) \(\newcommand{\xhat}{\widehat{\xvec}}\) \(\newcommand{\vhat}{\widehat{\vvec}}\) \(\newcommand{\uhat}{\widehat{\uvec}}\) \(\newcommand{\what}{\widehat{\wvec}}\) \(\newcommand{\Sighat}{\widehat{\Sigma}}\) \(\newcommand{\lt}{<}\) \(\newcommand{\gt}{>}\) \(\newcommand{\amp}{&}\) \(\definecolor{fillinmathshade}{gray}{0.9}\)Introduction
A Piping & Instrumentation Diagram (P&ID) is a schematic layout of a plant that displays the units to be used, the pipes connecting these units, and the sensors and control valves. Standard structures located on a P&ID include storage tanks, surge tanks, pumps, heat exchangers, reactors, and distillation columns. The latter three comprise most of the chemical process industry single-unit control problems.
P&IDs have a number of important uses in the design and successful operation of chemical process plants. Once a process flow diagram is made, P&IDs help engineers develop control strategies that ensure production targets are met while meeting all safety and environmental standards. These diagrams are also very important for locating valves and process components during maintenance and troubleshooting.
Each page of a P&ID should be easy to read and correspond to a specific action of the plant. Also, symbols used in the P&ID are uniform throughout. Diagrams for heat exchangers, continuously stirred tank reactors (CSTRs), and distillation columns shown in subsequent sections of this wiki represent a small sample of standard symbols for these structures. For a list and explanation of standard controls-related symbols, please refer to PID Standard Notation.
General Strategies for Implementation of Good Control Systems
There are several guidelines to follow when designing P&IDs for a plant. The first consideration is stable operation of the plant so that all safety and environmental standards are met. Maintaining product quality should also be a primary design objective. Additionally, systems should be designed to respond quickly to rapid changes in rate and product quality. Usually control systems should be run in an automatic mode so the system will correct itself, as opposed to a manual mode, which requires operator supervision.
When setting up a control system, it is useful to first focus on mass balance control, which can be monitored by level and pressure control loops that use gas or liquid flow rates. Additionally, a product control structure should be set up to ensure efficient process operation. To prevent controls from conflicting with one another, a final examination of the controlled streams should be performed. Further instrumentation can then be installed to prevent conflicts between controllers. Finally, appropriate tolerances should be established for controllers that directly affect the action of other controllers. Determination of the optimal control placement is essential for successful plant operation.
Standard Structures and Location of Control Features
As mentioned above, control of heat exchangers, reactors, and distillation columns represent the majority of single-unit control problems. The table below summarizes the control schemes derived in the following examples. The most common control schemes are listed in the table below.
Table 1: Summary of common P&ID structures
For most equipment, a degrees of freedom analysis is first performed and then control scheme is designed based on the degrees of freedom.
Heat Exchanger
To monitor the performance of a heat exchanger, the product stream is important. Usually, the product stream must be within some temperature range before it continues to downstream process units. The outlet temperature of this stream can be used to calculate the heat transfer. The steam is controlled in order to obtain the desired product stream temperature. One way to influence the product temperature is by controlling the flow of the heated steam. This flow-based control may take some time to implement and therefore cause fluctuations in the process. Depending on the process, these fluctuations may or may not be acceptable. Instead of monitoring the flow-rate, the steam pressure may be monitored, achieving tighter control of temperature. A change in pressure is much easier to monitor and correlates directly with a change in temperature of the steam. This offers an effective way to control process temperatures. Pressure control also enables the physical condition of the piping to be monitored, since pressure changes occur as fouling progresses. The pressure, combined with the flow-rate and temperature of the heated steam, can be used to calculate this fouling occurring inside a piece of equipment. It is important to remember that the steam should always be controlled on the inlet side of the heat exchanger for better pressure control and safety reasons, as shown in figure 1 below.
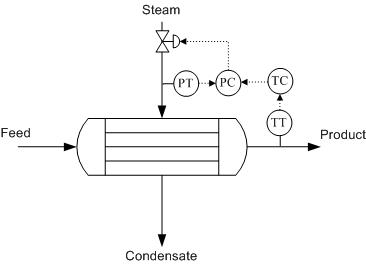
Distillation Column
Because the economic viability of an overall process is based significantly on product purity, it is important that distillation columns maintain stable operation. Changes in composition and flow-rate of the feed stream are common disturbances in distillation column operation. Improper functioning of controllers can undermine the effectiveness of the product composition. A degrees of freedom analysis can help place sensors and actuators in appropriate places, while not including too many sensors and actuators, in order to obtain an efficient control system.
Degrees of Freedom Analysis
A simple degrees of freedom analysis can make design of a control scheme easier as well as improve the control scheme overall. A process control approach to degrees of freedom, adapted from ECOSSE Module 3.1, requires tabulation of streams and extra phases.
DOF = Streams − ExtraPhases + 1
A typical distillation column contains the following streams; feed (1), bottoms (2), distillate (3), reflux (4), product (5), vapor-liquid mix (6), cooling water (7), and steam (8). There are also three locations where there are two phases, vapor and liquid, present in equilibrium. These are denoted as one "extra phase", since temperature and pressure are not independent in a two-phase system.
DOF = 8 − 3 + 1 = 6
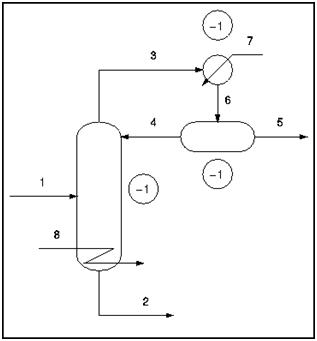
In typical practice, the condenser and reboiler pressure are specified as atmospheric pressure. Once the pressure is specified in the condenser and reboiler (both two-phase systems), the temperature is specified and therefore the degrees of freedom are reduced by two. The total degrees of freedom, in practice, is six.
DOF = 8 − 5 + 1 = 4
A simple degrees of freedom analysis, in any system, can help define the variables and reveal where the critical sensors for process control should be located. This type of analysis also minimizes the design of too many sensors, actuators, and valves, which may in theory control and regulate the same variable.
Sensor and Actuator Options
Product streams, reboiler steam, and the reflux stream should have flow sensor/transmitters so that each flow can be adjusted to meet the column’s control objectives. A flow sensor should also be placed on the feed stream because disturbance to the feed flow rate are common. Each flow sensor should be connected to a flow valve to control the corresponding stream.
Differential pressure level sensor/transmitters should also be used for the accumulator (the vessel that collects condensed distillate) and bottom of the column because maintaining these levels is essential for reliable operation of the column. If flooding is an issue, a pressure differential across the column should indicate the onset of flooding. A pressure indicator should be installed at the top of the accumulator to monitor column pressure. Temperature in a distillation column is typically controlled by manipulating steam flow to the reboiler.
Control Schemes
There are a number of common control schemes for distillation columns. Optimally, a distillation column should be run with dual composition control because it saves energy. In dual compostion control, the temperature of both chemicals in a binary distillation is controlled. The system is more complex to setup and measurements required for control may be difficult. As a result, many distillation columns use single composition control instead. Common control configurations for distillation columns include reflux-boilup and distillate-boilup.
In the reflux-boilup configuration, the distillate composition and bottoms composition are the control variables. The reflux flow and the heat input control (vapor boilup) are the manipulated variables, which allow control of the liquid and vapor flow-rates in the column. With this control system, a quick response to changes in the feed composition is possible. In the distillate-boilup control configuration, the distillate flow and the vapor boilup are used to control composition. This configuration is a better choice for columns where the reflux ratio is high.
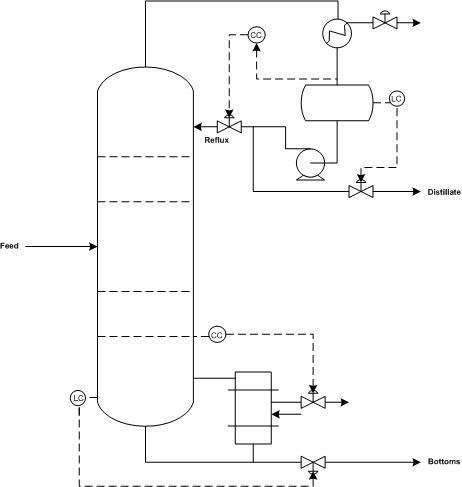
Reactor (Exothermic Reaction in CSTR)
In implementing controls in reactive systems, temperature is a good indicator for unit performance. Temperature is often related to reaction rate and varies with time in most reactors. However, a reactor exit stream with a constant temperature is often desired downstream in the process.
In an exothermic reaction in a CSTR, lower initial temperatures result in lower reaction rates and low heat generation. As the reaction progresses, heat generation increases rapidly due to higher reaction rates and high concentrations of reactants. As reactant concentration decreases, the heat generation once again becomes low. Exothermic reactor temperatures must be controlled to assure stable reactor operation.
To remove heat from an exothermic reaction, basic heat transfer principles are employed. A coolant is pumped through a shell outside of the reactor. Since the heat removal is linear, the temperature of the coolant should be controlled. In doing this, it is possible to increase the driving force for heat transfer to slow a reaction, or conversely, to allow the reaction to further progress by decreasing the driving force for heat transfer.
Degrees of Freedom Analysis
In order to determine where to place controls, sensors, and valves in a exothermic reaction operation, a degrees of freedom analysis, similar to that carried out in the distillation section 3.2, can be helpful.
A typical CSTR contains the following streams; reactant A (1), reactant B (2), product (3), and coolant to the jacket (4). There are no locations where there are two phases, vapor and liquid, present in equilibrium - assuming the reaction is liquid phase with no simultaneous evaporation or sublimation.
DOF = Streams − ExtraPhases + 1
DOF = 4 − 0 + 1 = 5
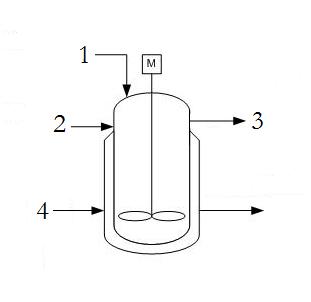
Since in most practical applications the reactants (1 and 2) as well as the product (3) flow rates are defined by demand for the product, there are only 2 degrees of freedom which allow for placement of a 2 valves or controllers on the coolant stream (4) as well as one of the reactant streams (1 or 2). Only one of the reactant streams need to be specified as the other can be determined by a ratio controller using stoichiometric coefficients.
Control Schemes
As discussed previously, a valve can be placed on the coolant inlet stream to ensure proper temperature control of the reactor. By controlling the coolant stream based on inlet conditions of the reactant streams, the control can respond quickly. But, if the coolant is controlled based on outlet conditions of the product stream, there is a lag in response, but it is easy to monitor heat transfer performance.
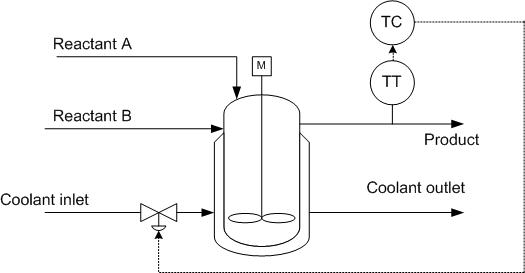
To translate this example to an endothermic reaction, the coolant flow would simply be translated to steam flow in order to provide heat to the reaction through the CSTR jacket.
Other Common Process Equipment
Beyond the heat exchangers, reactors, and distillation columns, many other pieces of process equipment, including furnaces, compressors, decanters, refrigerators, liquid-liquid extractors (LLEs), and evaporators, are subject to disturbances and require careful control.
Furnaces
For example, furnaces may be subject to frequent load changes as a process or customer requires more energy. To cope with these demands, the temperature of the outlet stream must be monitored and manipulated. Information from a temperature controller at the outlet stream can be used to effect changes in valves that control the flow-rate of air and fuel to the furnace. At this point, the best setup of the control system must be considered in light of factors such as safety, lag time for changes to occur, and equipment wear. For a furnace, the controls should generally be set up so that an excess of air is more likely than an excess of fuel. This reduces the risk of explosion due to the furnace filling with uncombusted fuel.
Liquid-Liquid Extractors
In liquid-liquid extractors, the interface level and pressure are the controlled variables. Disturbances in flow rate of the entering stream can affect interface level and prevent complete separation of the heavy and light components. From this, it is obvious that there should be valve controls on both exit streams. The best control scheme depends on the operation of the process. When the heavy phase is continuous (light phase flows upward through heavy phase), changes in interface level should be controlled by adjusting the flow-rate of the light product, while the pressure is controlled by adjusting the flow-rate of the heavy product out of the column. Figure A is a representation of what occurs in a single stage extractor. Generally, single stage extractors are using in chemical labs, where as multistage extractors are used in industry. A multistage extractor uses the immiscible liquid stream from the previous stage as the feed in the following stage. Figure 6 depicts the control scheme previously described.
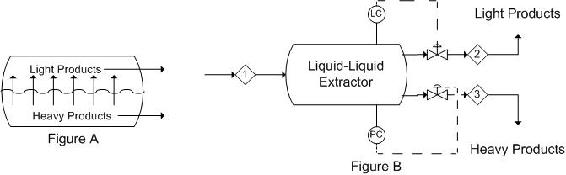
When the light phase is continuous, the control system must be set up in the opposite manner. Figure C is again a depiction of what occurs in a single stage extractor. Figure D is a representation of a control scheme that could be implemented. This is the reverse of the control scheme in Figure 6.
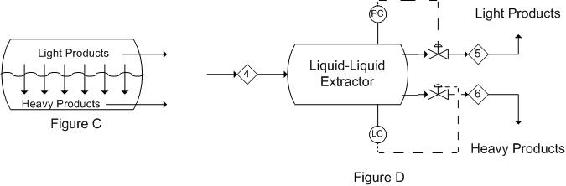
These representations are only two possibilities for basic control schemes that can be implemented in a process as there are several controllers and aspects of the specific processes that may need to be controlled or monitored.
Compressors
Compressors are another valuable component in process design. They allow for the reduction of the volume of an incoming stream by increasing the pressure at which the stream is maintained. They can also be used to pump liquids through the process, as liquids are highly incompressible compressors cannot be used for volume reduction. For this, there must be a specific control system as to prevent adverse effects due to extremely high or low pressures. There are several types of compressors, including: dynamic, axial, and rotary [1] to name a few. Because the increase in pressure is governed by the ideal gas law, there is most often and increase in temperature as well. This can be left as is, or sent to a heat exchanger for temperature reduction. Heat exchangers were discussed above.
One such example is the use of a centrifugal compressor to reduce the volume of a fuel stream for storage. Using a compressor will allow for volume reduction as gasses are easily compressed, this is also economically friendly as it reduces the size of tank necessary to store the fuel stream. The tank should also be equipped with a pressure reducing valve, to bring the stream back to a desired pressure, depending on the process. A diagram of this scheme is as follows:
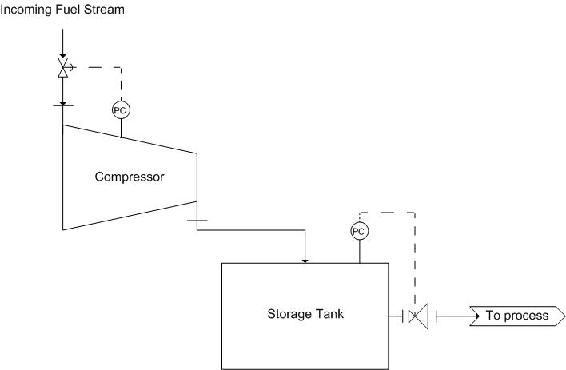
The pressure controller on the compressor controls the valve on the incoming fuel stream. This ensures that if there is a build up in pressure, the flow into the system will be stopped in time. Also, a pressure controller should be placed on the storage tank. This is controlled by the pressure reducing valve mentioned earlier.
Decanters
Decanters, much like Liquid-liquid extractors, use solubility as their principle of separation. Unlike Liquid-liquid extraction, these require some time for the separation to occur. Generally, the separation is a liquid-liquid or liquid-solid separation. Decanters are widely used in the wine industry to separate out sediment from the wine. Utilizing the wine separation example, a possible control scheme is as follows. Here, there is only a level sensor on the decanter as it is a liquid-solid separation. Note that there is a release stream, used to remove collected sediment. An analytical or pH sensor could also be used here to maintain the correct chemistry or pH, as wine is the final product. It is also important to note that the exact placement of the level sensor would vary depending on the desired level in the tank. Here, the level sensor is not shown in its exact placement.
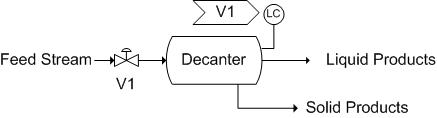
Another vessel that is very similar to decanters are knockout drums. These vessels are generally located after heat exchangers or other pieces of equipment that result in a multiphase system. These vessels are used to separate the two phases, generally gas-and liquid separation. A possible control scheme is depicted below. The incoming stream is a liquid-gas mixture coming from a heat exchanger. Thus, there is a pressure sensor on the knockout drum. A level controller could be used, but this is effectively measuring the same thing, so it has been omitted. Also, because it is coming from a heat exchanger, a temperature controller has been included to control the amount of cooling taking place in the heat exchanger.
The pressure controller (PC) controls V2, the stream into the tank. The temperature controller (TC) controls V1, the valve on the coolant stream to the heat exchanger.
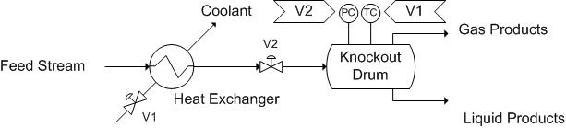
These examples illustrate the typical method of locating control systems for process equipment. After choosing the location for valves based on process constraints, there still remain a number of possibilities for the actual manner in which to control the valves. The lag-time for changes may be longer for certain configurations, while the danger of damaging equipment is smaller. The controls configuration will depend strongly on the safety concerns associated with a specific process.
Selecting Controls and their Locations for a Multi-Unit Process
The following steps should be followed when setting up controls for multi-unit processes. For more in-depth descriptions, refer to the Step-by-Step Method For Describing Controls and Their Purpose.
- Determine process objectives, taking into consideration product specifications, economic constraints, environmental and safety regulations, etc.
- Identify boundaries for normal operation. These can be based on equipment limitations, safety concerns, environmental regulations, and the economic objectives of the processes.
- Identify units and streams in the process that are susceptible to significant disturbances. These disturbances commonly occur in feed streams, product streams, and reactor vessels, but can be present anywhere that temperature or pressure or other variables are changing.
- Select the types and locations of sensors in order to properly measure and monitor critical process variables.
- Determine the appropriate types and locations for control valves in order to appropriately adjust process variables so that they remain within the normal operating boundaries. Controls should be set up to minimize response time between sensing a change and taking corrective actions. The ideal location for any given control depends on the process unit or units that it affects.
- Perform a degree of freedom analysis.
- Energy Considerations. An energy balance should be performed for the process. This step involves transporting energy to and from process units. This may include removing heat generated by a reactor and using it elsewhere in the process. Control valves will help regulate the flow of such streams.
- Control Process Production Rate and Other Operating Parameters. Adjusting process inputs, such as reactant feed rates, can alter other variables in the process. Process controls must be able to respond to these adjustments to keep the system within operating boundaries.
- Set up control system to handle disturbances and minimize their effects. (See Chemical Process Controls > PID Control)
- Monitor Component Balances. Accumulation of materials within a system is not desirable and can lead to inefficiency in the process or catastrophic failure.
- Control individual unit operations. Each unit of a multi-unit process needs to be individually controlled in order for control of the entire system to be possible.
- Optimize the process. If the system has degrees of freedom, process variables can be manipulated in order to more efficiently or economically create product.
Consider the following reaction in a semi-batch reactor:
\[\ce{(CH3CO)2O + H2O -> 2CH3COOH} \nonumber \]
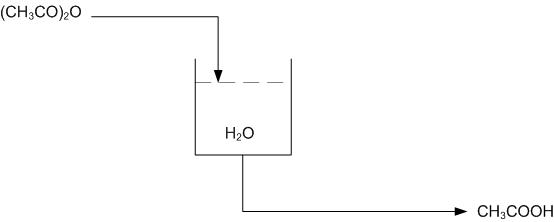
The objective is to produce \(\ce{CH3COOH}\) at a given concentration, i.e. 15-20%. The tank should also be drained once the given concentration is achieved and the reaction has gone to completion. The tank can only hold a specified volume and 80% is filled with water. The reaction should be run in excess water. Once a given amount of acetic anhydride has entered the reactor, it should be left in the tank until the reaction has gone to completion. The completion of the reaction can be determined by temperature, as the reaction is exothermic.
Using the multi-unit controller design from above, determine the location of needed sensors and valves on the flow diagram.
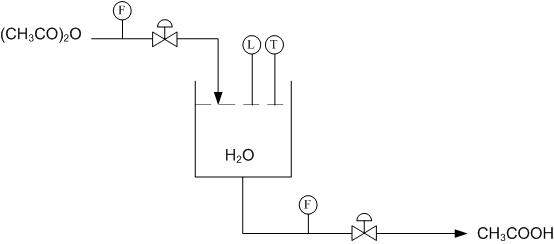
Using Figure E-2 determine how to use the level and temperature sensors to limit the amount of acetic anhydride entering the reactor and also how to drain the system once the reaction has gone to completion.
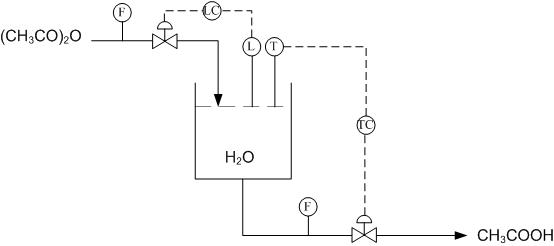
Using the above system, when the right amount of acetic anhydride has entered the reactor the level sensor will stop the flow into the reactor. Once the reaction has gone to completion and the temperature sensor has been triggered, due to a peak in temperatures from the exothermic reaction, the tank will drain.
Examine the figure below, which shows two different control schemes for a heat exchanger. The outlet stream temperature must remain constant. How is this goal accomplished using the control systems shown below? Which stream is the manipulated stream? What are the advantages and disadvantages of each setup?
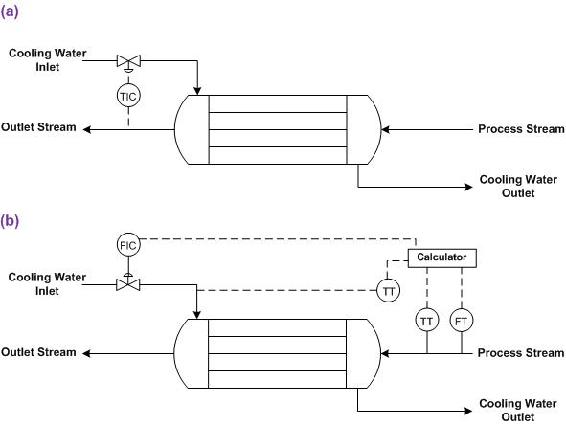
Solution
In both setups, the cooling water flow is manipulated to control the temperature of the outlet stream. The control strategy for each heat exchanger is different.
Figure E-4 (a) shows a heat exchanger where the flow of cooling water is adjusted based on the temperature of the outlet stream. The advantage to this setup is that it is quite straightforward and the cause of the change in the temperature of the outlet stream does not have to be identified. The disadvantage is that a temperature change has already occurred before action is taken, and if the lag-time for the additional cooling water to cool the process stream is long, the outlet stream temperature may be inconsistent.
Figure E-4 (b) shows a heat exchanger were the flow of cooling water is adjusted based on the flow-rate and temperature of the inlet stream and the temperature of the coolant stream. Based on a set of calculations using the heat transfer coefficient of the heat exchanger, the outlet stream temperature can be predicted. The advantage of this system is that action is taken before changes occur in the outlet stream temperature. The disadvantage is that if the actual heat exchange capacity differs from the expected value due to fouling or mechanical problems, the outlet temperature will not be correct.
This presents an alternate notation of controls. The arrows above the controller indicate what parts of the process that the controller controls.
\[\ce{A + B -> AB} \nonumber \]
- B is added slowly into a full charge of A
- The temperature is maintained at TR (RXN temperature)
- Upon completion of reaction, AB is cooled to TP
- C is added to AB to make final product, which leaves the tank
Solution
- LC1: This controls M1 and V1.
This controller is used to keep the level of A in the A tank above a preset minimum.
- LC2: This controls M2 and V2.
This controller is used to keep the level of B in the B tank above a preset minimum.
- LC3: This controls M3 and V3.
This controller is used to keep the level of C in the C tank above a preset minimum.
- FC1: This also controls M1 and V1.
This controller totalizes the amount of A that has flowed out of the A tank, and turns off flow when the flow amount has reached a preset value.
- FC2: This also controls M2 and V2.
This controller totalizes the amount of B that has flowed out of the B tank, and turns off flow when the flow amount has reached a preset value.
- FC3: This also controls M3 and V3.
This controller totalizes the amount of C that has flowed out of the C tank, and turns off flow when the flow amount has reached a preset value.
- LC4: This controls V1, V4, M4, and M5.
V1 - If level of liquid in the reaction tank goes over a preset maximum, V1 is closed.
V4 - If level of liquid in the reaction tank goes under a preset minimum, V4 is closed.
M4 - If level of liquid in the reaction tank goes under a preset minimum, M4 is turned off.
M5 - If level level of liquid in the reaction tank goes under the level of the agitator, M5 is turned off.
- TC1: This controls V3, V5, and M3.
M3, V3 - If the temperature in the reaction tank is at TP, M3 is turned on and V3 is opened.
V5 - To maintain the temperature in the reaction tank at TP, V5 is opened and closed accordingly.
References
- Bequette, W.B. Process Control Modeling Design and Simultion., New Jersey: Prentice Hall, pp 466-477
- Luyben, W.L. Plantwide Process Control., New York: McGraw-Hill, pp 53-69, pp 201-203, pp 235-247
- Module 3.1: Control of Distillation Columns. The ECOSSE IGDS Controls HyperCourse. University of Edinburgh, Scotland.
- Ogunnaike, Babatunde A. Process dynamics, modeling, and control, New York: Oxford University Press 1994, pp 1149-1153
- Riggs, James B. Chemical and Bio Process Control., Ferret Publishing, pp 491-504
- Turton, Richard. Analysis, Synthesis, and Design of a Chemical Process, New Jersey: Prentice Hall, pp 408-409
- U.S. Chemical Safety and Hazard Investigation Board; "Morton International Explosion." www.csb.gov/completed_investigations/docs/mortondigest.pdf. Last Updated 07/17/2003.
- Tompkins, Bill. "Reaction and action." www.ehponline.org/members/2004/112-6/focus.html. Last Updated 09/09/2007
- Wikipedia. "Gas Compressors" http://en.Wikipedia.org/wiki/Gas_compressor. Last Updated 11/27/2008
- Wikipedia. "Liquid-Liquid Extraction" en.Wikipedia.org/wiki/Liquid-liquid_extraction. Last Updated 11/20/2008
Contributors and Attributions
- Authors: Christopher Bauman, Jennifer DeHeck, Merrick Miranda, Evan Leonard
- Stewards: Robert Chockley, Chloe Sweet, Irene Brockman, Scott Dombrowski
- Anchors: Megan Boekeloo, Stacy Young