10.3.1: Bioethanol
- Page ID
- 85157
\( \newcommand{\vecs}[1]{\overset { \scriptstyle \rightharpoonup} {\mathbf{#1}} } \)
\( \newcommand{\vecd}[1]{\overset{-\!-\!\rightharpoonup}{\vphantom{a}\smash {#1}}} \)
\( \newcommand{\id}{\mathrm{id}}\) \( \newcommand{\Span}{\mathrm{span}}\)
( \newcommand{\kernel}{\mathrm{null}\,}\) \( \newcommand{\range}{\mathrm{range}\,}\)
\( \newcommand{\RealPart}{\mathrm{Re}}\) \( \newcommand{\ImaginaryPart}{\mathrm{Im}}\)
\( \newcommand{\Argument}{\mathrm{Arg}}\) \( \newcommand{\norm}[1]{\| #1 \|}\)
\( \newcommand{\inner}[2]{\langle #1, #2 \rangle}\)
\( \newcommand{\Span}{\mathrm{span}}\)
\( \newcommand{\id}{\mathrm{id}}\)
\( \newcommand{\Span}{\mathrm{span}}\)
\( \newcommand{\kernel}{\mathrm{null}\,}\)
\( \newcommand{\range}{\mathrm{range}\,}\)
\( \newcommand{\RealPart}{\mathrm{Re}}\)
\( \newcommand{\ImaginaryPart}{\mathrm{Im}}\)
\( \newcommand{\Argument}{\mathrm{Arg}}\)
\( \newcommand{\norm}[1]{\| #1 \|}\)
\( \newcommand{\inner}[2]{\langle #1, #2 \rangle}\)
\( \newcommand{\Span}{\mathrm{span}}\) \( \newcommand{\AA}{\unicode[.8,0]{x212B}}\)
\( \newcommand{\vectorA}[1]{\vec{#1}} % arrow\)
\( \newcommand{\vectorAt}[1]{\vec{\text{#1}}} % arrow\)
\( \newcommand{\vectorB}[1]{\overset { \scriptstyle \rightharpoonup} {\mathbf{#1}} } \)
\( \newcommand{\vectorC}[1]{\textbf{#1}} \)
\( \newcommand{\vectorD}[1]{\overrightarrow{#1}} \)
\( \newcommand{\vectorDt}[1]{\overrightarrow{\text{#1}}} \)
\( \newcommand{\vectE}[1]{\overset{-\!-\!\rightharpoonup}{\vphantom{a}\smash{\mathbf {#1}}}} \)
\( \newcommand{\vecs}[1]{\overset { \scriptstyle \rightharpoonup} {\mathbf{#1}} } \)
\( \newcommand{\vecd}[1]{\overset{-\!-\!\rightharpoonup}{\vphantom{a}\smash {#1}}} \)
\(\newcommand{\avec}{\mathbf a}\) \(\newcommand{\bvec}{\mathbf b}\) \(\newcommand{\cvec}{\mathbf c}\) \(\newcommand{\dvec}{\mathbf d}\) \(\newcommand{\dtil}{\widetilde{\mathbf d}}\) \(\newcommand{\evec}{\mathbf e}\) \(\newcommand{\fvec}{\mathbf f}\) \(\newcommand{\nvec}{\mathbf n}\) \(\newcommand{\pvec}{\mathbf p}\) \(\newcommand{\qvec}{\mathbf q}\) \(\newcommand{\svec}{\mathbf s}\) \(\newcommand{\tvec}{\mathbf t}\) \(\newcommand{\uvec}{\mathbf u}\) \(\newcommand{\vvec}{\mathbf v}\) \(\newcommand{\wvec}{\mathbf w}\) \(\newcommand{\xvec}{\mathbf x}\) \(\newcommand{\yvec}{\mathbf y}\) \(\newcommand{\zvec}{\mathbf z}\) \(\newcommand{\rvec}{\mathbf r}\) \(\newcommand{\mvec}{\mathbf m}\) \(\newcommand{\zerovec}{\mathbf 0}\) \(\newcommand{\onevec}{\mathbf 1}\) \(\newcommand{\real}{\mathbb R}\) \(\newcommand{\twovec}[2]{\left[\begin{array}{r}#1 \\ #2 \end{array}\right]}\) \(\newcommand{\ctwovec}[2]{\left[\begin{array}{c}#1 \\ #2 \end{array}\right]}\) \(\newcommand{\threevec}[3]{\left[\begin{array}{r}#1 \\ #2 \\ #3 \end{array}\right]}\) \(\newcommand{\cthreevec}[3]{\left[\begin{array}{c}#1 \\ #2 \\ #3 \end{array}\right]}\) \(\newcommand{\fourvec}[4]{\left[\begin{array}{r}#1 \\ #2 \\ #3 \\ #4 \end{array}\right]}\) \(\newcommand{\cfourvec}[4]{\left[\begin{array}{c}#1 \\ #2 \\ #3 \\ #4 \end{array}\right]}\) \(\newcommand{\fivevec}[5]{\left[\begin{array}{r}#1 \\ #2 \\ #3 \\ #4 \\ #5 \\ \end{array}\right]}\) \(\newcommand{\cfivevec}[5]{\left[\begin{array}{c}#1 \\ #2 \\ #3 \\ #4 \\ #5 \\ \end{array}\right]}\) \(\newcommand{\mattwo}[4]{\left[\begin{array}{rr}#1 \amp #2 \\ #3 \amp #4 \\ \end{array}\right]}\) \(\newcommand{\laspan}[1]{\text{Span}\{#1\}}\) \(\newcommand{\bcal}{\cal B}\) \(\newcommand{\ccal}{\cal C}\) \(\newcommand{\scal}{\cal S}\) \(\newcommand{\wcal}{\cal W}\) \(\newcommand{\ecal}{\cal E}\) \(\newcommand{\coords}[2]{\left\{#1\right\}_{#2}}\) \(\newcommand{\gray}[1]{\color{gray}{#1}}\) \(\newcommand{\lgray}[1]{\color{lightgray}{#1}}\) \(\newcommand{\rank}{\operatorname{rank}}\) \(\newcommand{\row}{\text{Row}}\) \(\newcommand{\col}{\text{Col}}\) \(\renewcommand{\row}{\text{Row}}\) \(\newcommand{\nul}{\text{Nul}}\) \(\newcommand{\var}{\text{Var}}\) \(\newcommand{\corr}{\text{corr}}\) \(\newcommand{\len}[1]{\left|#1\right|}\) \(\newcommand{\bbar}{\overline{\bvec}}\) \(\newcommand{\bhat}{\widehat{\bvec}}\) \(\newcommand{\bperp}{\bvec^\perp}\) \(\newcommand{\xhat}{\widehat{\xvec}}\) \(\newcommand{\vhat}{\widehat{\vvec}}\) \(\newcommand{\uhat}{\widehat{\uvec}}\) \(\newcommand{\what}{\widehat{\wvec}}\) \(\newcommand{\Sighat}{\widehat{\Sigma}}\) \(\newcommand{\lt}{<}\) \(\newcommand{\gt}{>}\) \(\newcommand{\amp}{&}\) \(\definecolor{fillinmathshade}{gray}{0.9}\)People have learned how to produce ethanol several thousand years ago. The method was simple – make a pulp out of ripe grapes, put it into a clean vessel, and wait. Grapes contain sugar – most fruits do, it’s their method of storing energy. In grapes there are three varieties of sugars, two simple known as glucose and fructose, and one complex, sucrose, whose molecule consists of one glucose and one fructose molecule.
On the grapes’ skin, there is always yeast – a simple organism single-cell organism, a member of the large kingdom of fungi. Yeast feeds on sugars, the energy it acquires from that is used for multiplying the cells. The simplified chemical formula for both glucose and fructose is C6H12O6. When the grapes are pulped, the yeast comes into direct contact with the sugars. They start to process them – what’s happen is called the ethanol fermentation
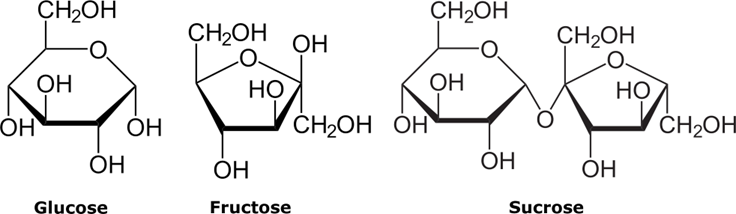
The process involves several steps catalyzed by some yeast enzymes, but the overall chemical reaction can be written as:
\[ \mathrm{C}_{6} \mathrm{H}_{12} \mathrm{O}_{6} \longrightarrow 2 \mathrm{C}_{2} \mathrm{H}_{5} \mathrm{OH}+2 \mathrm{CO}_{2} \]
where C2H5OH is the chemical formula of ethanol. The fermentation of sucrose is a bit more complicated – first, the yeast uses an enzyme to split the molecule into one glucose and one fructose molecule, and then process them in the same way as described above.
What is created as the result of fermenting grape juice is wine. The final product usually contains 12%-13% of ethanol. Long time ago, our ancestors discovered that drinking wine brings good mood (sometimes, even too good a mood). So, wine has become an important ingredient in the cultures of many tribes living in areas where grapes can be grown.
But many people lived in regions where the climate was not favorable for grape growing. Apples and berries growing in the north were not good precursors for fermentation. Therefore, German tribes, Slavic tribes, British tribes could not enjoy the benefits of wine. But they invented something else. They learned how to ferment starch products.
Mono-, Bi-, and Poly-saccharides
Glucose, fructose, sucrose and starch are all members of a great family of saccharides. Glucose and fructose are called monosaccharides because their molecules are just single saccharide “unit” (the third monosaccharide “sibling” is galactose). As can be seen in Fig. \(\PageIndex{1}\), in the monosaccharide molecules there are many -O-H groups, sprouting out of a carbon atom
They are called hydroxyl groups. What may happen is that two hydroxyl groups, each from a different monosaccharide molecule, get together, “jet- tison” one H2O molecule, and leave one oxygen atom which now links to two carbon atoms, each one belonging to a different “parent ” molecule (it’s referred to as an “oxygen link” or an “O-link”). In Fig. 10.6 the glucose and the fructose molecules are linked by such an O-link, forming the sucrose molecule. Sucrose is the main component of table sugar. But there are many other combinations of two monosaccharides coupled by the same mechanism – for instance, lactose made of glucose and galactose – we certainly know it all because it’s one component of human milk. But there many other possi- ble combinations of two monosaccharides, and all of them together make a sub-family called disaccharides. In the Wikipedia article linked as many as 18 such combinations are listed.
If two can be linked, why not three, four, ...? Yes, they can. Groups made up from 3 to 10 O-linked monosaccharides re called oligosaccharides – from oligo, meaning “a few” in ancient Greek language. And even larger groups are called polysaccharides. And starch is perhaps the best known representative of the latter category.
Many plants create starch as an energy-storing substance by O-linking several hundred glucose molecules into chains – either a single chain, called an amylose chain, or a main chain with several sub-chains branching out – forming a molecule of amylopectin. In each form, all glucose units are kept together by O-links. Per average, forming an O-link costs each glucose molecule one molecule of H2O, so that the overall chemical formula for amy- lose or amylopectin is (C6H10O5)n, with n of the order of several hundred for amylose, and up to 200,000 for amylopectin.
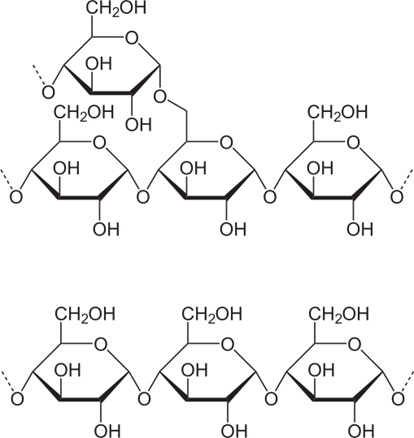
History Continued
As noted, the northern tribes did not have fruits rich in sugar that could be easily fermented. They did have plant products rich in starch, though – but the bad news is that yeast does not agree to ferment starch. Monosaccharides and disaccharides – yes, happily, but starch – no way!
Nonetheless, the norther tribes did find a way to obtain ethanol from starch. The key to success was barley, a cereal grain rich in starch – one of the first grains cultivated by humans. The northern people discovered that if barley grains were soaked with water for a short period, then dried and left for some time – they started tasting sweet! The sweet component could be extracted from the grains using hot water, and water solution of sugars obtained in this way could be fermented. And the product of fermentation was nothing else than beer.
The first part of this recipe is now called malting . What exactly happens in this process? When barley is for the first time soaked with water, the grains start germinating. In the early stage of germination the grains get ready to convert starch into another form of an “energy carrier”. Why? Well, because soon the energy will be needed in new parts of the plant growing out of the grain. And starch is a material non-soluble in water. How to get it out of the grain? Mother Nature had found an ingenious trick: convert starch to sugars that are water soluble, and then “pump” the solution to the sprout and to the emerging stalk and root system.
So, in the early stage of germination an enzyme called amylase is produced in the grains. Its task is to convert the starch into sugars. The enzymes are essentially catalysts – they allow a chemical reaction to occur, but they are not “consumed” by it. So, if the germinating process is terminated at the right moment – with amylase already there – the enzyme will continue to do its work, as long as there is still any starch remaining. But the sugars will stay in the grain. One should give the malting process enough time to be completed – and the next step is to extract the sugar from the grains. One can do that by immersing the grains into hot water. The sugar gets dissolved in water, and then the sugar solution, after separating it from the grains’ leftovers, can be fermented by adding yeast for obtaining beer as the final product.
With time, the process was further refined. Beer typically contains 3%- 5% of ethanol. The next invention was to use distillation of the fermented malt – by such an operation, one can increase the ethanol concentration about tenfold: this is how whisky is produced (the technology was developed around the year 1200, and without much change has been used until today). Other people discovered that the enzymes from germinating barley can be added to starch from other plants – e.g., from potato. The enzyme converts the starch to sugar, yielding a syrup-like product known as molasses. It can fermented by adding yeast – and after distillation, one obtains a final product with 40% - 50% of ethanol, known as vodka. By making further improvements to the distillation technique – much credit for that should be given to medieval alchemists – people learned how to obtain a distillate with ethanol concentration up to 95%. It is commonly referred to as spirit. It’s not something one would like to drink, but it has many other applications – as a solvent, or as a disinfectant.
It is also worth mentioning that in some p;arts of the world where sugar cane grows, the process of making vodka may be much simpler. The juice pressed out from the cane contains sugar, so one can skip the process of enzymatic conversion. By fermenting the sugar cane juice and applying distillation, on obtains a product known as rum. At some period rum from Caribbean Islands and Middle America became perhaps the most popular alcoholic beverage. Around 1800 it was transported to destinations even as distant as Australia. In order to economize the transport – sailing from Ja- maica to Sydney could take six months or more – the rum was sent out as a concentrate, with about 80% of ethanol – and after reaching Sydney, it was diluted by adding the same volume of water.
Bioethanol as a Fuel
Why did we pay so much attention in the preceding section to the methods of producing ethanol? Well, the answer is simple: when the demand for transportation biofuel has emerged for the first time, no new technology was needed – the existing distilleries simply had to start cranking out more product. But the method remains essentially the same.
Brazil has been the pioneer in biofuel production. As far as the total volume manufactured is concerned, it was the world leader until 2006 – and it still is the world leader in imposing bioethanol fuel economy. One helpful factor that has enabled Brazil to attain this position is the fact that all Brazilian bioethanol is made from sugar cane. Like in the case of rum production, the labor end energy consuming process of enzymatic conversion can be skipped. Therefore, the Brazilian bioethanol has a competitive price and a very favor- able energy balance:
\[ \text{energy balance = \dfrac{\text{energy balance}}{\text{energy input} \]
the average of which is 8.3 for the entire industry, and 10.2 for the newest installations.
Currently, there are no light cars running on pure gasoline in Brazil. Currently, the minimum ethanol content in the fuel blend is 27% (E27). But the “flex” vehicles that dominate the market of new cars can run on fuel consisting of any proportion of gasoline and alcohol, including pure hydrous1 ethanol (E100).
The United States is presently the larger manufacturer of bioethanol fuel, with the output twice larger than that of Brazil.
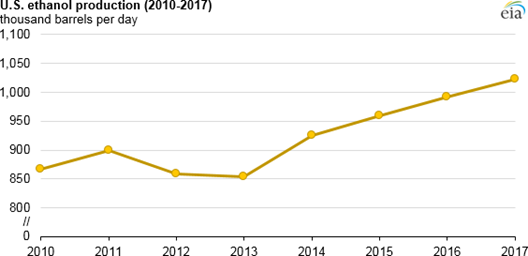
In the US, over 99% of biofuel is made from corn (maize). Currently, two major techniques are used: wet milling and dry milling. In the former, the grain kernel is separated into its components (germ, fiber, protein, and starch) and then only the starch is further processed – like in the “classical” recipe of vodka making. The latter is a newer process, in which the grain kernels are first ground into flour – then the process is continued the same way as for pure starch, and the non-fermentable parts are removed only at the later stage of the process. Now most of the operating facilities in the US use the dry milling technique.
There is one sad truth about American corn ethanol that should be made clear. Above, it was mentioned that the average energy balance of Brazilian sugar cane ethanol is 8.3, and in the newest production facilities it is as high as over 10. But for American corn ethanol the value is a miserable 1.3. The Author of this text does not want to make any comment – the Reader is kindly asked to draw her/his own conclusion.
What is the corm biofuel made by American distilleries used for? Ten percent of bioethanol is now mandated to be blended into gasoline in most American states. Lowering the CO2 emission is one goal, but perhaps a more important reason is that ethanol acts as an anti-knocking agent and as a oxygenate. Anti-knocking additives enhance the octane number of gasoline, and oxygenates cause that the gasoline burns more completely, thus reducing the tailpipe emission. It is expected that soon E15 will be mandated, i.e., a blend with 15% of ethanol. But a significant reduction of CO2 the E85 blend is recommended. It is already available in some states, but it can be used only by cars with “flexible fuel” engines – at present, only about 10% of all cars in the US are equipped with such engines.
The data shown in Fig. \(\PageIndex{3}\ indicate that currently there is a clear growing tendency in the production of corn biofuel in the US. However, as follows from a recent analysis, it is hard to expect that eventually there will be enough alcohol to replace most of the gasoline used by Americans. Currently, over 40% of all corn grown in the US is used for making alcohol – with the output approaching 20 billion gallons per year. But the country uses over 130 billion gallons of gasoline, and over 50 gallons of diesel fuel per year. Therefore, even if 100% of corn is used for making fuel, it will be only enough to replace 25-30% of all the petroleum needed by the entire American transportation.
Well, this is not a very optimistic perspective... People and farm animals need to eat something, so even 25-30% is not a realistic figure. Is there any remedy for such a gloomy forecast? Yes, there is. Corn is not the only raw material for making ethanol that is available in the US. Stay tuned, please!
More Polysaccharides – Cellulose and Hemicellulose.
Earlier in this chapter it was mentioned that plants photosynthesize CO2 and H2O to make sugars, starch, and what else? Cellulose! The third photo- synthesis product is cellulose, a material used to make cell walls, and stalks needed to grow high. In a ripe corn plant, there is more cellulose than starch and sugar combined.
Is it possible to make ethanol from cellulose? Yes, definitely, because cellulose is made of the same “building blocks” as starch, i.e., of glucose molecules. The structure of cellulose is more complicated, though. The structure of amylose, the linear starch molecule, is shown in Fig. \(\PageIndex{2}\). Note that all glucose molecules forming the chain are aligned in the same way.
Cellulose also consists of linear chains of glucose molecules connected by the “O-links” – with one small but essential difference: look at the upper chain in. Fig. 10.9 and imagine that every other glucose molecule is “turned upside down” – in other words, is rotated by 180◦ around the chain’s long axis – as in the chain below.
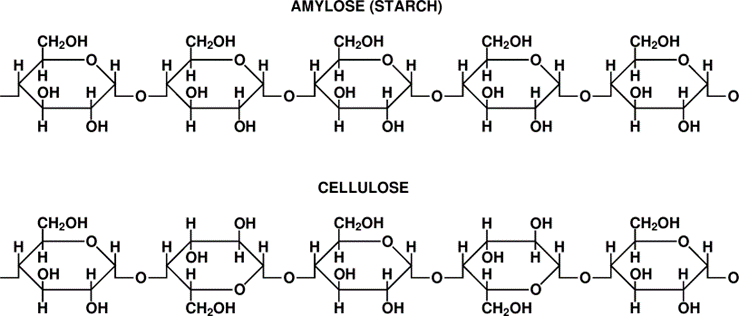
It is instructive to make a model of a single cellulose strand using small plastic balls, as shown in Fig. \(\PageIndex{5}\. Here the black ball symbolize the carbon atoms, the red balls – the oxygen atoms, and the small gray ball – the hydrogen atoms. The rods connecting the atoms represent the chemical bonds – the so-called covalent bonds which are the main type of coupling that binds atoms in organic molecules together.
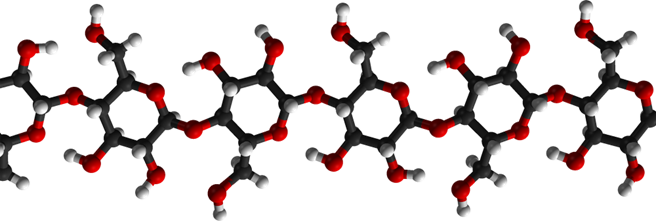
The physical mechanism of covalent bonding is such that each one of the two coupled atoms contributes to the binding one electron from its outer electronic shell, and these electrons are “shared” by the two atoms. The electrons in the outer shell are referred to as the valence electrons. Carbon has four of them, therefore it may be coupled with as many as four other atoms. Oxygen has two valence electrons, and hydrogen only a single one.
In Fig. 10.11 there are two parallel elementary cellulose chains. What can be seen in this figure is that some of the hydrogen atoms from the “upper” chain get pretty close to the oxygen atoms from the “lower” chain – and vice versa. Between these hydrogen-oxygen pairs there are small orange two- headed arrows. What do they represent?
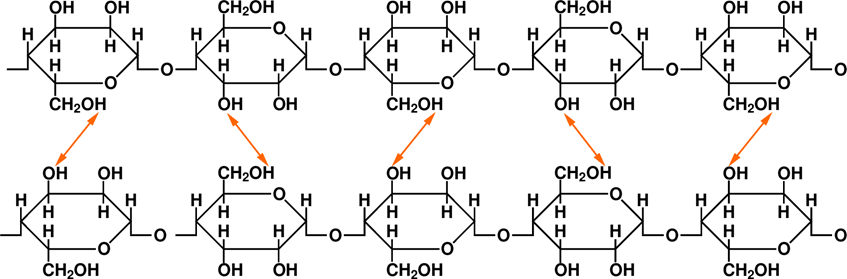
The H and O atoms forming an -OH group – such combination is commonly referred to as the hydroxyl group – are coupled by a covalent bonding, meaning that both H and O contribute one electron and then they “share” the electron pair. But you know how it often is with sharing... Oxygen in this partnership behaves like the proverbial “big brother” – well, let’s not go too deep into details, but the truth is that the two electrons are not equally shared by H and O, but they spend more time closer to the O atom than to the H atoms. So what happens? Well, the O atom effectively acquires a bit more negative charge than it normally has, and the H atom has a bit less negative charge than it normally has. Atoms normally are neutral, right? So, effectively the H atoms becomes positively charged, and the O atom becomes negatively charged. And as we know very well, positive and negative charges attract each other, it’s called the Coulomb interaction. Consequently, due to the attractive forces between individual H-O pairs, there is a net Coulomb coupling between the two chains over their entire length.
But can only two chains get coupled? Of course not! Each chain in Fig. \(\PageIndex{5}\) may get couple to another chain, these “new” chains to more chains, effectively forming a sheet – well, not necessarily, a sheet may be changed to a fiber by rolling it in such a fashion that the elementary glucose chains are parallel to the fiber axis. Such fibers have a crystal structure – i.e., they represent a highly ordered arrangement of atoms with clear periodicity.
One cellulose fiber contains over 10 000 elementary glucose molecules and is up to 5 micrometers long. From fibers one can make a great variety of good things, as we know. Most of the clothing we wear is made of fibers. Of different kinds, yes, but anything made of fabric is made of fibers.
Cellulose is the main “construction material” that plants use for building objects with a variety of sizes, from cell walls whose dimensions are of the order of a micrometer (10−6 m) to tree trunks that in some species (such as, e.g., redwood) reach the height of 100 meters. However, fibers alone can not give plant tissues all necessary rigidity. To attain that, plants combine cellulose fibers with three other structural components: hemicellulose and pectin, which are polysaccharides, and lignin, which is a complicated biopolymer whose structure is not related to sugars.
In this text the interest is focused on biomass that is of potential use for making biofuels. Biomass containing pectins (such as, e.g., hay) has a high value as forage. But there many other “biomasses” that cannot be fed to animals – many kinds of residues e.g., straw, corn or soybean stover, bagasse (what remains after sugarcane is crushed to extract sugar) left after harvesting – as well as sawdust or wood chips. They all contain cellulose and hemicellulose which can be, at least partially, converted to biofuels. For instance, dry corn stover contains about 70% of cellulose and hemicellulose, and 15-20% of lignin. In softwood and in hardwood the proportions are pretty similar. Biomass for making fuels have not necessarily be residues, there are some plants worth growing with the intention of using them whole – here, much attention is paid to s witchgrass which does not require good soil and much water, but grows up to 10 feet tall and may yield several tons of biomass per acre.
Cellulosic Ethanol – History
Cellulose and hemicellulose are the two components that can be converted to ethanol. There are several existing technologies, some of them low-tech and some high-tech. The first commercial production of cellulosic ethanol started 120 years ago in Germany. Wood chips were treated with sulphuric acid H2SO4 at elevated temperature, which causes a “hydrolysis” of polysaccha- rides – i.e., their decomposition to elementary sugars. The resulting “soup” consists of acid + dissolved sugars + lignin. The latter is not affected by the hydrolysis process and can be later filtered off. The acid can be neutralized by adding crushed limestone, which is nearly pure calcium carbonate CaCO3. It reacts with sulphuric acid, yielding calcium sulfate:
\[ \mathrm{CaCO}_{3}+\mathrm{H}_{2} \mathrm{SO}_{4} \longrightarrow \mathrm{CaSO}_{4}+\mathrm{H}_{2} \mathrm{O}+\mathrm{CO}_{2} \]
which has a very low solubility in water and precipitates from the solution. What remains is a solution of sugars – and now it can be processed the same way as the sugar solution in the techniques of making alcohol from sugar cane or from starch: just by adding yeast and fermenting the sugars. After gaining experience, before the outbreak of World War One the German installations were able to produce up to 50 gallons of ethanol from one ton of sawdust or wood chips. It was called “wood ethanol” and was definitely not good for human consumption because of some nasty contaminants, but it was pure enough to be used in industrial chemical processes or as a solvent.
During World War One the US industry needed a lot of ethanol, so the technology was “imported” from Germany and even though the American installations yielded only about 20 gallons from a ton of wood chips, the total volume of the wood ethanol made in America soon became much higher than that made in Germany. Later, also the American technology was gradually improved and reached the German yield of 50 gallons per ton. During the World War Two years wood alcohol was a crucial ingredient for manufacturing synthetic rubber – it was badly needed regardless of the price. But the price was pretty high, so the production plants were shut down shortly after the war.
In fact, the process of decomposing cellulose into sugars has been known for millions of years before humans started experimenting with it. Wood, as we know (sometimes from sad experience that may cost a homeowner thousands of dollars!) is the food of termites. To be more accurate: the cellulose in wood is what they eat. And larger animals – cattle, sheep – can also feed on a cellulose-rich diet. Well, not exactly: they all employ much smaller “workers” to deal with cellulose – it is, microbe cultures living in their intestines. No large animals can digest cellulose directly. Only some microbes and some fungi can. And because they have been doing that for many hundreds millions of years, the Author believes that it is a right thing to put this piece of information into the “History” subsection.
Cellulosic Ethanol – Today
As noted, the acidic hydrolysis of cellulose was a costly procedure and there fore, once there was no more emergency, it has been abandoned. Well, but if microbes and fungi can decompose cellulose, why cannot we try a similar method – perhaps it will be a cheeper alternative?
The microbes and fungi use enzymes. The generic name for a cellulose- degrading enzyme is cellulase. There is a whole variety of them already discovered, and research on them is continuing, so even more of them may be identified in the near future. As all enzymes, cellulases are proteins. Some of them can decompose cellulose and hemicellulose into individual monosaccharides; some other may cut the cellulose chain into longer oligosaccharides consisting of several sugar molecules. From the viewpoint of cellulosic ethanol production, the most interesting are those which convert the cellulose and hemicellulose macromolecules into fermentable sugars.
Efforts of developing practical technologies of producing cellulosic ethanol involving enzymatic hydrolysis have intensified in the opening years of the 21st century. The first step is to prepare the material – in the biomass the cellulose chains are entangled with lignin and hemicellulose. Such structures have to be broken, in order to assure an “easy access” to the cellulose chains and hemicellulose complexes for the enzymes. Only them may be the en- zymes administered – and after they finish their work, the resultant “soup” of sugars can be further processed by yeast, and then distilled to extract the ethanol. A nice graph illustrating the first few steps in the cycle is shown, for instance, in this Web site. As far as the “preparation stage” is concerned – of liberating the polysaccharide chains from the access-blocking wrapping of lignin – several different methods can be used. One possible pre-treatment method uses dilute acids. Another possible approach is to use the so-called “steam explosion”. In short, the biomass is packed into a container which is next filled with hot steam of pressure many times higher than the atmo- spheric pressure. The steam penetrates the biomass and fills all the voids in the dead plant tissues. Next, the container is suddenly opened, so that the high-pressure steam, seeking an escape from the voids it has drifted into, rips apart the biomass structure. How such “steam explosion pretreatment” works is illustrated in in this NC State University publication – see, in particular, the Figure 11 – or, (for even more details, see pages 10-11 in this report from the Danish Technological Institute).
But enzymatic decomposition is not the only possible process. Recently, Renmatix, a Pensylvania-based company, has developed a technology in which only “water and temperature” is used for decomposing the cellulose and hemicellulose into elementary constituent sugars. The details of the processes used are explained in the company’s Web site. When the page opens, click first on the icon TECHNOLOGY – and then, on the Plantrose process, to get a verbal description of the technology – and next, on the WATCH FULL VIDEO icon. In short, the technology the company uses makes it possible to separate xylose sugars from glucose.
A few words about the xylose sugars we have not yet paid much attention to. Cellulose, as has been discussed above, consists exclusively of glucose molecules linked into long chains. But in hemicellulose glucose is only a small fraction of the constituent molecules – the majority are molecules of xylose sugar. In contrast to other monosaccharides found in plants (glucose and fructose), the molecules of which contain six carbon atoms, xylose molecule contains only five carbon atoms. There are several other five-carbon sugars in living organisms, and the generic name for them is “pentose sugars”.
In the he sugar “soup” obtained by enzymatic decomposition of biomass glucose is the dominant component, but there is also a significant fraction (20-30%) of xylose from the hemicellulose. And in the next step of biofuel production – the fermentation – xylose is only a “neutral bystander”, because no known strain of yeast can process five-carbon sugars. It’s not surprising: over hundreds of millions of years the yeast fed only on fruits and other plant elements containing monosaccharides and disaccharides, but had little chance to encounter anything containing pentose sugars. So, Mother Evolution or whoever else was taking care of teaching the yeasts what was “good” and what was “not good for eating” did not see any need to teach them to feed on such sugars. But the good news is that this problem may be solved by high-tech biotechnology – it turns out that by modifying their genes some yeast strains can be “educated” to ferment xylose as rapidly as glucose.
Cellulosic Ethanol – Summary
The above subsections on cellulosic ethanol may pay a rosy picture of that technology: there is no need to use corn for making fuel for automobiles – it’s immoral! – more than 10% of people in today’s world suffer from hunger!.
It turns out that instead of using edible parts of corn for making biofuel, we may produce the same amount of it from corn’s stover, i.e., the nod-edible parts of it. And there are plenty of other sources of cellulose – switchgrass which grows well on lands of low agricultural value, wood debris, even municipal waste.
So, the potential is enormous – and what is being done? – the sad truth is that the situation with cellulosic ethanol is no better than one hundred years ago.
The enthusiasm for cellulosic ethanol was high in the first decade of this century and the mood in the US Government was pretty optimistic. The Energy Policy Act of 2005 created a Renewable Fuel Standard (RFS) for the U.S. The act created mandates ruling how much bioethanol from different sources had to be blended into gasoline in the years to come. However, while the corn ethanol was doing not so bad, the cellulosic ethanol completely failed to meet the expectations. The standards for it, which went into effect in 2010, mandated as many as 5.5 billion gallons in 2017. Yet, the actual production in 2017 reached only a pathetic 10 million gallons – even though two years earlier, in 2015, the nameplate capacity of all cellulosic ethanol facilities was 88 million gallons per year (for more details, please see this document; and the actual production data for the years 2010-2018 are given in this official EPA document). Why did the situation worsen so badly? Well, it seems – because of a conflict between the expectations and the brutal laws of market economy. The nameplate 88 million gallons in 2015 came from adding up the capacities of three facilities – but two of them went bankrupt since then. And what about the future? One can only “wait and see.” So far, it’s petroleum who is the king, and it does not seem likely that it will voluntarily abdicate in a foreseeable future.
__________________________________________________________
1To blend with gasoline, the ethanol must be anhydrous,i.e., contain no water. How- ever, the ethanol obtained by conventional distillation of water-ethanol at normal pressure cannot concentrate alcohol above 95.6%, because at this concentration the mixture becomes an azeotrope. So, what distilleries sell as “alcohol” is in most cases a mixture of 95% of ethanol and 5% of water; the proper name for it is rather “hydrous ethanol” – and this is precisely what the Brazilian E100 blend is