10.1: The Theory of Grasping
- Page ID
- 14830
The theory of grasping is quite involved, with the state of the art comprehensively described in (Rimon & Burdick 2019), yet has difficulties to mathematically exactly capture the mechanics of grasping mechanisms that are successful in practice. Rather than describing these developments here — which will be well beyond the scope of this book — we will briefly describe different approaches to model grasping, and their limitations, to provide a better understanding of what the reasons for grasps that work are and what matters when designing a gripper.
In its most simple form, grasping requires immobilizing an object, at least agains the forces of gravity, by providing appropriate forces in the opposite direction, also known as constraints. Specifically, contact points on a robotic finger, gripper or hand are assumed to exert localized forces, thereby constraining the object sufficiently. By this, fingers act essentially as miniature robotic arms, allowing us to apply the methods and tools from previous chapters 2–??
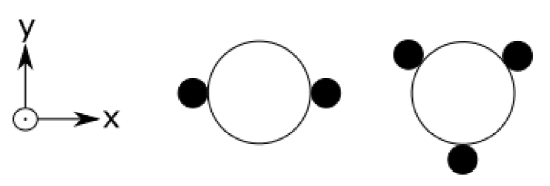
10.1.1. Friction
While already very involved for anything but very simple mechanisms, such a model only captures a very small slice of realistic grasps. In any real application, contacts between a gripper and hand are not friction-less. This is the reason a grasp such as shown in Figure 10.1 actually works. If there were really no friction between the fingers and the object, the object would be ejected from the hand for every grasp that is not exactly aligned with a principal axis of the cylinder in Figure 10.1, left. Furthermore, even the three-finger grasp shown in Figure 10.1, right, would always fail as there is no force constraining the object from below. Fortunately, the existance of friction makes grasping much easier in practice, yet much harder to describe mathematically.
The reason that the grasps shown in Figure 10.1.1 do work in most circumstances is that the normal forces shown have a tangential component that is due to friction and covered by Coloumb’s Friction law, which states that the higher the friction coefficient of a material, the more normal force translates into tangential forces that can resist two surfaces from moving against each other:
It is governed by the equation:
\[F_{t}\leq \mu F_{n}\]
Here Ft is the force of friction exerted by each surface on the other and Fn is the normal force. The force Ft acts in tangential direction of the normal force applied by, e.g., a finger’s tip, where µ is an empirical coefficient of friction.
The friction coefficient µ is low for glass on glass and high for rubber on wood. We are therefore interested in designing grippers with high friction coefficients to avoid objects from slipping.
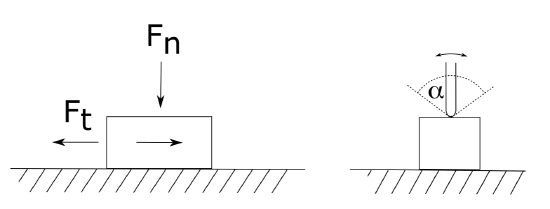
When do objects slip? Lets say we have a fingertip pressing down on a surface in any orientation. There will be a force normal to the surface Fn, which defines the tangential force Ft in any direction. Sweeping the tangential force around the normal force creates a cone with an opening angle of
\[\alpha =2tan^{-1}\mu\]
see (Rimon & Burdick 2019, p. 57) for a derivation. If the net force on the object is not within this cone, the object slips. This becomes more intuitive when thinking about how different values of µ affect the shape of this cone. If µ is high, the cone will be relatively flat, letting the object accept forces from many different directions without slipping. If µ is low, the cone will be relatively narrow, requiring the force to be normal to the object’s surface to prevent slippage.
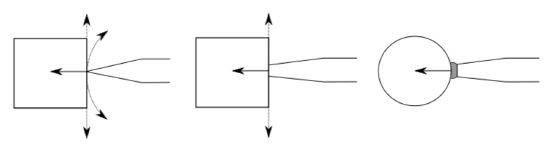
A force applied to a rigid body will exert both a force as well as a torque to the body’s center of gravity. This is called a wrench. If we consider all the possible forces and torques that we can apply to a rigid body without having the end-effector slip to form a space (namely the cone described earlier for a single finger), we can talk about the grasping wrench space, which is the corresponding space of all suitable wrenches.
Knowing the relation between normal and tangential reaction forces can help in designing grippers that are more likely to successfully grasp an object than others, as well as when planning suitable grasp for objects with known friction.
10.1.2. Multiple Contacts and Deformation
In practice, no force will ever be applied at a single point only, but over an area, either due to the size of the finger pad itself or due to the contact area deforming. Even the smallest contact area that is not a point in the mathematical sense will add constraints on torque, thereby adding constraints in additional dimensions and therefore further stabilizing the grasp. This is illustrated in Figure 10.1.3. Whereas the object can easily pivot around the point of contact in Figure 10.1.3, left, increasing the area of contact constrains the rotational degree of freedom. It is therefore desirable to grasp an object with an as large contact area as possible. As surfaces are not ideally flat, in practice this is only possible when the contact area is deformable, Figure 10.1.3, right. A large contact area will also increase friction, which is usually desirable.
Indeed, using blank metal jaws or fingers is little successful in practice. Instead, rubber pads are used to increase force closure by conforming around the object. As the rubber is flexible, however, the grasp is not completely fixating the object, but it can move within the grasp, which might not be desirable when picking up a nut, e.g., and trying to mount it on a screw. Mathematically, this introduces additional complications into the grasp model, as flexible pads are the equivalent of a spring, increasing uncertainty and dynamics.
10.1.3. Suction
A highly capable method for grasping is using suction. Here, a suction cup is pressed against an object, using a vacuum applied by a pump to suck the object against the cup. Instead of exerting forces against the object, which always requires at least one antipodal force (or multiple forces that are distributed such that the object remains in equilibrium) to create a constraint, suction only requires one point of contact. The rim of the suction cup provides both friction and multiple contact points to prevent the object from slipping and further constraining the object beyond the normal force applied by the vacuum. Requiring only a single area of contact is a tremendous advantage from a planning perspective as only one area on an object needs to be identified, whereas other grasping approaches need to always identify two areas and coordinate motion to reach them. (Suction using multiple suction cups on custom-made rigs to grasp large car parts such as doors is very popular in the car industry, but relies on preprogrammed trajectories, which is not a focus of this book.)
The soft nature of the suction cup provides the ability for the rim to conform to the object to some extent, but makes suction impractical for objects that do not have any flat surfaces or holes, for example objects stored in a net. The elasticity of the rim also makes it difficult to further manipulate the object as all forces applied by the robot will need to be transferred via a spring-like elastic material. Finally, suction requires a vacuum pump that is able to generate sufficient force to lift an object, limiting the maximum weight of objects suitable for suction by a single suction cup in practice.